Case study: Production process optimization in order to increase efficiency and to reduce workload
● Reduced workload ● Faster production ● Fewer employees ● Smaller space requirement
In this current blog post, you can read a summary of one of our case studies, where we provided production line screening and process optimization. We present the steps and results of this project. You can download the detailed case study at the end of this blog post.
The client had to grapple with constantly high fluctuation rates and the production process was slower than expected. The aim was to detect and eliminate bottlenecks and at the same time to check workloads in order to secure compliance with the standard EN 1005-4. In the course of the project, we reviewed the work instructions, monitored workflows, and measured the cycle time for each operation. Further, we inspected the intensity of workloads and checked whether suitable tools were available. We examined whether the material flow between different parts of the production line supported optimal production conditions.
The results of the survey and our optimization recommendations have been simulated and analyzed with the ViveLab Ergo software allowing us to compare the original and the planned work processes. Thus, we were able to prove the success of the optimization proposal before realization and to calculate the return on the investment. Thanks to the modification of workstation layout and the reallocation of tasks we reduced the workload, increased the speed of the conveyor belt by 15%. We also reduced the number of employees at the cable box assembly station and reduced the space requirement of the pre-assembly line to 58%.
STEP 1: SCREENING, I.E. ERGONOMIC IMPACT ASSESSMENT
During the screening, the workstations on the production line are going to be categorized according to the intensity of workloads along with the seriousness of health effects and involved risks.
This first phase is important in order to be able to assess the overall state of the production area as quickly as possible and to see where the problem is most acute, where corrective measures are needed immediately.
The deficit map was interpreted together with the management and we selected those workplaces where the recording of movements with sensory motion capture equipment followed by analysis using the ViveLab software was required.
Due to the complexity of the issues identified in this case study we would like to highlight only one of the problem areas. We are going to describe below the optimization of a pre-assembly line that represented a bottleneck in the production line. It took the longest time to complete that component part of the end product which was manufactured here. It had an adverse effect on the whole production process because it was not possible to increase the speed of the conveyor belt on the main production line. In order to be able to increase the speed of the conveyor to the extent as the customer requested, the pre-assembly line should have released a new product every 44 seconds instead of the original 51 seconds.
STEP 2: MOTION CAPTURE WITH SENSORY EQUIPMENT
In order to be able to locate accurately the problem in the pre-assembly unit and to determine how to fix it, we needed objectively measured data. Therefore, the movements of the workers on the pre-assembly line were captured with 17 wireless inertial sensors fixed on their bodies. These sensors can be calibrated quickly and easily without hindering the production. They do not impede or influence the movements of the body, so employees can move naturally and do their job as usual.Unlike optical sensors, there is no need for a camera system. Thanks to the Xsens Motion Capture technology, electromagnetic waves do not distort data.
In the course of this process we recorded the 5 different workflows in about two hours. With this step our task in the production area was completed. Data analysis is always carried out outside the production area at the office of our experts.
STEP 3: VIVELAB ERGO SIMULATION AND ANALYSIS
Secret HungaryLtd.could not provide the CAD model of the workstations. Based on the floor plans, we had to build up the pre-assembly line from geometric primitives. The simple model of the work environment we got this way was in this case sufficient to subject the working process at different workstations and their interfaces to diverse ergonomic analysis methods.
After we had constructed the environment, we created virtual human characters and assigned to each character the relevant motion files that had previously been captured by the sensors. Asa result, we had finally a digitized model of the pre-assembly line and of the work activity there.
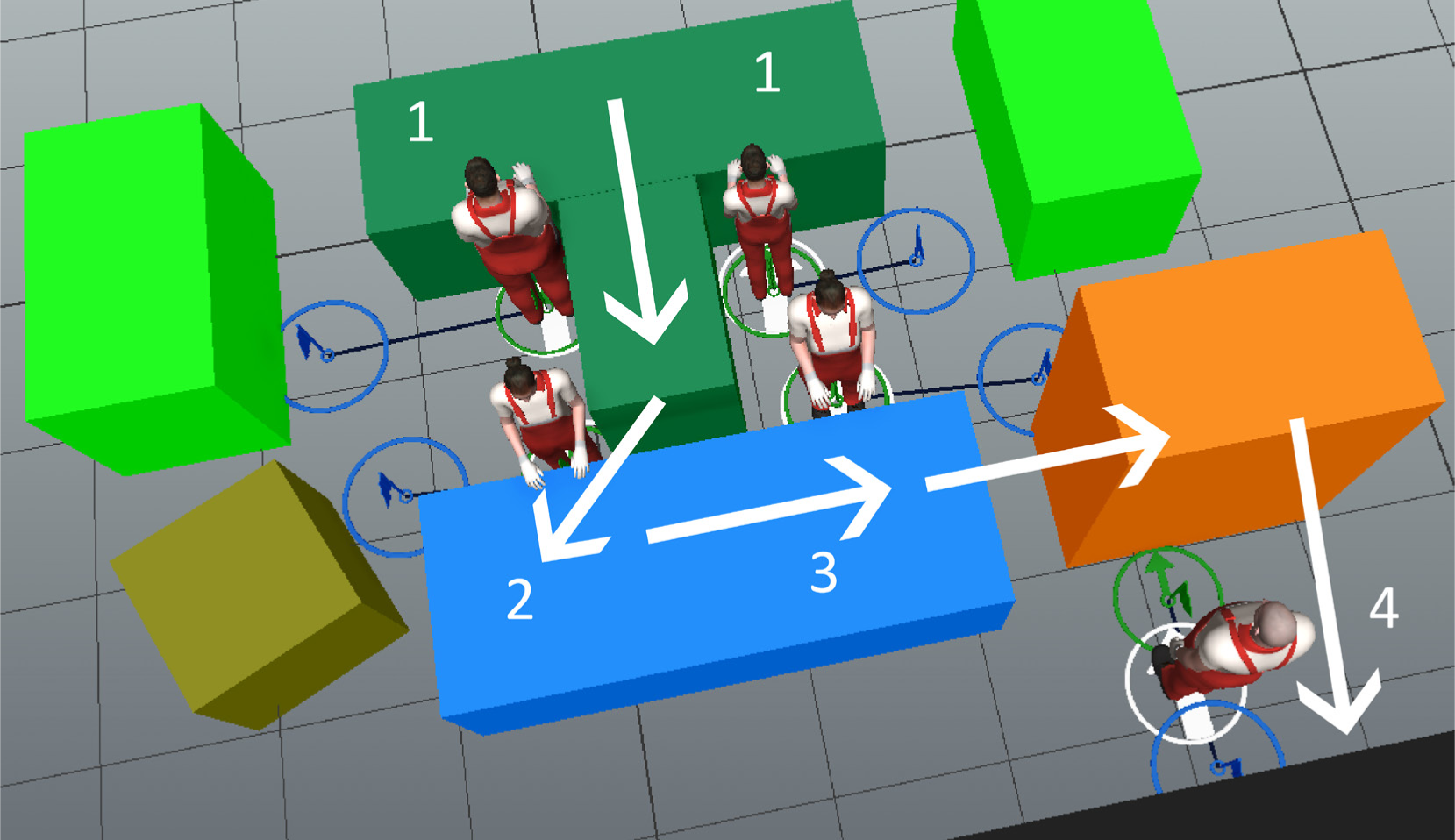
Thanks to the accurate capturing of motion, the built-in analyses methods also detect those critical movements and postures that might not have been noticed without the sensors or that might have remained hidden because of potential screening effects. For the purpose of a detailed investigation, we have exported the analysis reports that highlight with relevant angles and with accuracy of hundredths of a second those positions that need to be adjusted to reduce the workload of employees.
Analysis results based on the ViveLab Ergo report
The software evaluates the postures of the employees according to seven built-in ergonomic analyses tools: RULA, OWAS, NASA-OBI methods, ISO 11226, EN 1005-4 standards,Spaghetti Diagram and Reachability Test. The software checks whether the load on each body part exceeds the acceptable limit.
We examined what kind of health-harming postures occur often and which movements slow down the work process significantly. While examining the motions, we identified those movements that were not utterly necessary for the successful completion of the task and looked for ways to avoid them.As a result, we were able to reduce the cycle time and it was possible to speed up the conveyor belt.
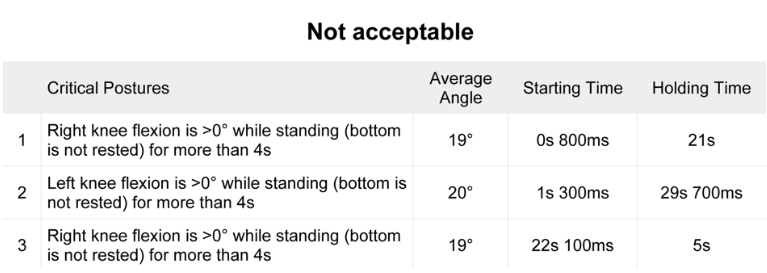
Description of the identified problems in general
One of the biggest problems we have discovered was the scarcity of space. As a result, it was difficult to access the different parts of the workstations, it was impossible to find a suitable place for the supply containers, the employees often hampered each other’s movements, the tools and fittings were rather encumbrance than help.
Although the employees had to move lightweight workpieces, this had to be done at a high frequency, which is nonetheless harmful for the musculoskeletal system. There was a mess on the tables because of the badly organized material handling and employees obstructed each other’s way.
It has been found to be a serious problem that working in a standing position can cause muscle pain and fatigue and can lead to musculoskeletal disorders on the long term. Due to the poor design of the working environment, objects were difficult to grasp and move, which was causing joint pains in the hands. Uncomfortable and strained postures, such as bending forward to take the necessary items from the container or leaning over the table during installation, were common. In addition, the hands were regularly raised even above the shoulder.
We found basic size and dimension fitting problems regarding the design of the workstations. Working heights were not appropriate. The height of the supply containers did not meet the requirements either. Therefore, it was very difficult for the employees to complete their task and they had to take on postures that were harmful to their health in the long run. Reachability problems were common. The workers had to stretch far and wide for certain tools and parts. We found that the placement of tools and parts was irrational. These were difficult to access and were located at a distance from the employee. Employees wasted precious seconds walking and reaching for different parts and tools. Unnecessary movements made the workers tired and in many cases they had to take inconvenient postures.
High frequency movements and sustained uncomfortable static postures occurred in many cases. As shown in the figure below, the wrist joint was heavily stressed because the hand was raised or tilted sideways during a high percentage of the cycle time.
STEP 4: TECHNICAL DESIGN, VIRTUAL VALIDATION
The report, that was exported from the software, clearly shows those movements that are physically demanding or avoidable. This report, which is based on accurate and objective measurements, provides essential data for the design team of engineers and ergonomics experts. On this basis, our specialists develop an action plan that includes several possible individual, organizational and technical proposals. We recorded the appropriate motion files for the selected new layout and simulated the new workflows. After analyzing the results, we were convinced that the cycle time would indeed be shorter and that the workload would be reduced.
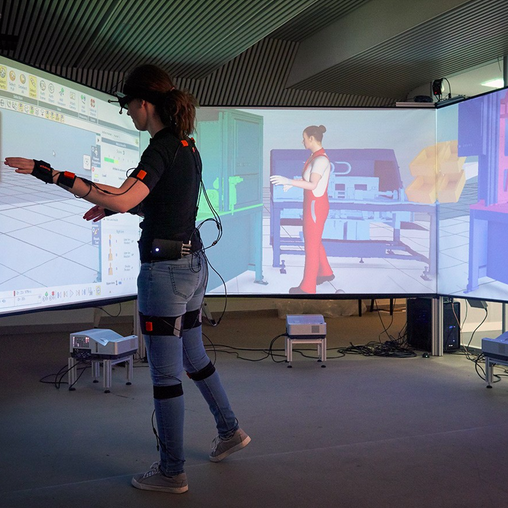
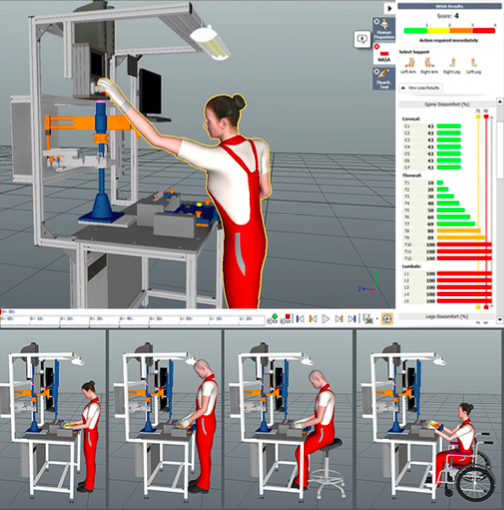
Instead of working on two larger workbenches as previously, each employee works at his own height-adjustable desk on the new pre-assembly line. This allows them to work at a table suitable to their own height. The advantage of this solution is that they are all able to carry out their tasks in the most comfortable manner and they get less tired during work. As a result, the muscles of the neck, shoulders and spine of the worker are less strained. He is going to feel fatigue later and he can maintain high productivity. We can expect that in the second half of the shift his performance will not slow down and he is going to make fewer mistakes.
We recommended that the employees should be given a chair so that they could alternate between working in a standing or sitting position, which is also supported by the height-adjustable desk. The chair they use should also have wheels so that they can easily roll closer to the container or to the conveyor belt.
We have proposed the installation of roller bar conveyors between the different workplaces for the transfer of items to be assembled. In this way the employees have to raise less weight and they can simply push the workpiece to the next table. Another benefit of the new arrangement is the elimination of clutter on the desktop that was previously caused by the accumulation of component parts for several new items on the table.
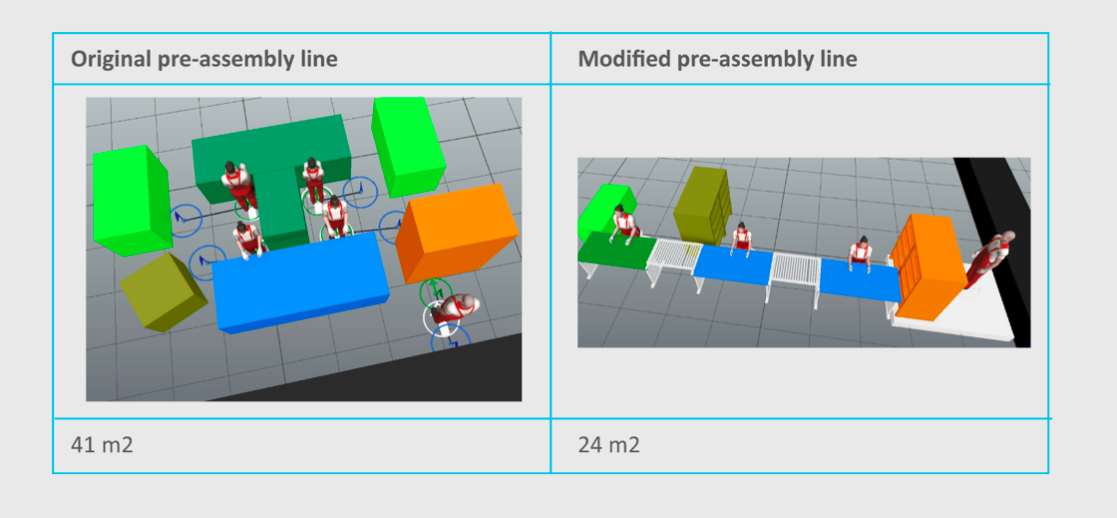
We have also rationalized the method how tools and parts are stored. It can be seen in the picture that the supply containers are placed closer to the workers and consequently, they can reach more easily the necessary parts. According to the new work organization, the light green supply container and some smaller storages on the desktop (that are not visible for confidentiality reasons) are going to be filled by the pre-production line supplier instead of the person working at the workstation. The orange container gets filled by employee No. 3. This is where the pieces completed on the pre-assembly line are stored. Normally only one or two shelves of the orange container are going to be filled because the worker No.4 continually takes the pieces and assembles them with the pieces arriving on the conveyor of the main production line. The other shelves remain in most cases empty. However, if for some unforeseeable reason the conveyor belt of the main production line stops, the orange container, that is substantially larger than necessary, makes it possible to store more pieces. Consequently, the pre-assembly unit does not have to stop.
PROJECT RESULTS
The entire project from the on-site screening until the technical design and virtual validation took approximately 12 working days. The most important result of the corrective measures was that it reduced the cycle time in the pre-assembly unit. In this way we could achieve the goal that had been set by the customer. It became possible to speed up the conveyor belt as it was requested. The time required to produce the final product has been reduced as well. The speed of the conveyor belt has been increased by 15% compared to the original speed. This faster production process increases the annual revenues of the company approximately by 250 000 Euro.
Thanks to the reorganization, one employee instead of two can fulfill the task at the cable box assembly workstation and yet the production is faster. As a consequence, the worker can be moved to another area where there is a shortage of workforce. This is going to save approximately 15 000 Euro annual wage costs for the company.
In addition, supplying the line with raw materials has become much smoother. The space requirements of the workstations have been reduced from 41 m2 to 24m2, which means that the space requirement has been reduced to 58%.
We tested with the ViveLabErgo software the redesigned workstations according to the same ergonomic analysis methods as we had done in the case of the original workplaces. The report exported from the software details the analysis results for each workstation. From this document the RULA analysis results are compared below.The financial gain achieved by protecting the health of workers is harder to quantify. Preventing musculoskeletal disorders also means financial savings, as the cost of sick leave days is significantly reduced.
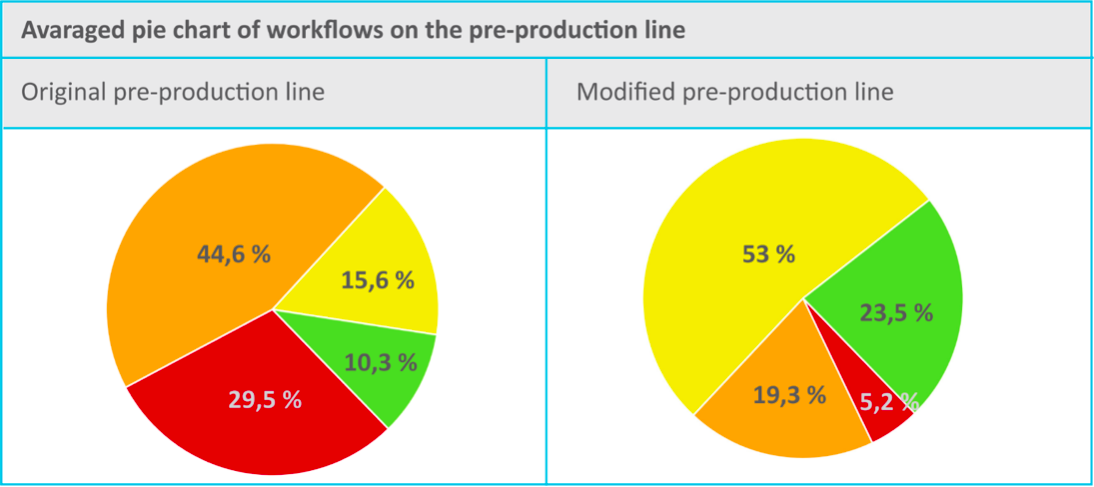
As one can see from the charts, the proportion of postures that pose long-term health risks has been significantly reduced. In parallel, the proportion of healthy postures has increased. This example illustrates that significant results can be achieved with a few simple modifications when we want to reduce the workload for the employees.
Like the original workstations, the redesigned ones were examined according to the NASA method, and tested according to the ISO 11226 and EN 1005-4 standards. Every analysis method proves that the redesigned workflow is much less burdensome for employees.
We consider it to be an outstanding achievement that we were able to secure the compliance with the strict requirements of the EN 1005-4 Work Safety Standard, which examines the posture and movement of workers in relation to the machine during work.
CONCLUSION
The example presented here demonstrates how can, based on the results of a detailed ergonomic study, a successful redesign of a workstation or of a complete manufacturing unit reorganize the workflow and improve the efficiency of an entire factory. It is a huge achievement in itself that with fewer workers production is yet faster and production space is reduced, but it is invaluable that the employer has done everything he can to prevent musculoskeletal disorders. This will make the company more attractive than its competitors. As a result of the changes we have brought about, workers will be less exhausted by the end of the shift. Musculoskeletal disorders are going to be less common. In addition, ergonomically designed workplaces help the company to keep the workforce, as everyone likes to work in a workplace where the tasks can be carried out comfortably.
Download our detailed case study to learn more about each step of the project, the used methods, and the results of the survey!