Our latest project aimed to improve working conditions in a lollipop manufactory. The company is a small, family-like business that values the workers on the production line. Since some members had leg and backproblems, the owner asked our help to form ideas for improvement. The process of an hour cycle consists of several repetitive tasks and some lifting and carrying steps.
ViveLab Ergo performed an ergonomic impact assessment on the workstations of the lollipop-making process. We inspected the production area and recorded our observations taking into account many ergonomic aspects. In the production, all processes were low risk, so in their case, only "small changes are needed".
We found that the layout, the moving and carrying of the sugar, and environmental conditions have the potential for improvement. In the sugar preparation phase bending low positions and working over shoulder height occur, while the movement of the sugar is manual. On the production line, necessary working heights alter on a wide range. While in the packaging, a task-specific place should be defined for the boxes and the hampers.
Sensory measurements followed the impact assessment to find the places where small changes are to be issued. Two workers, a lady, and a gentleman dressed up in the motion capture sensor set. By their involvement, we recorded the motions belonging to the production tasks. Three steps of the sugar preparation, six of the production line, and two of the packaging process.
In the lollipop project, the production process was divided into three sections as follows:
In the sugar preparation phase, we suggested the use of aspecial cart to make easier the moving and carrying of sugar, and even the installation to the stretching machine. With that bending forward and even over shoulder height positions become avoidable, causing less load for the spine,the arms, and shoulders.
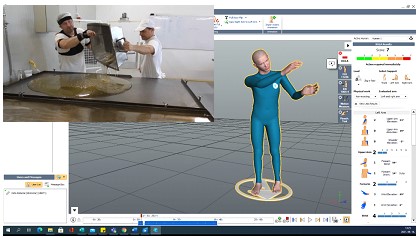
On the production line, seven work positions were recorded and assessed. To get a working height that fits all of them, we suggested using saddle chairs to scale the working height and decrease the load caused by purely standing work. This solution also decreases the probability of back and neck problems.
In the last phase, the lollipops are put in small boxes that are put in cartons. The suggestion was to form complete packing workstations with the elements in suitable places to avoid bending and twisting positions and even lessen the need for concentration.
Read our case study of our work in the lollipop factory.