Future of work - What is going to happen to workplaces after the fourth industrial revolution
The question of how the fourth industrial revolution is going to affect the labor market is becoming increasingly important today. Although it is believed that digitalization can lead to the loss of many jobs, it is still questionable how exactly this process will take place. However, it is certain that technological development is going to significantly change production processes in the manufacturing and processing industries as well.
As a consequence of the changes that were brought about during recent years the human-robot collaboration, which is gradually replacing the classical human-machine cooperation, is becoming more and more widespread and it is creating new challenges for both employers and employees. By applying appropriate design principles development can result in more efficient, comfortable and safer working conditions. However, to successfully work with robots it is important to consider already during the planning phase the potential hazards and the ergonomically proper coordination of the human and technical factors. During the ergonomic analysis of workplaces those work processes are revealed in which the automation and the application of robotics pay off from the point of view of the employees. Examples include extremely repetitive or monotonous work processes or those that require high levels of physical effort from employees.
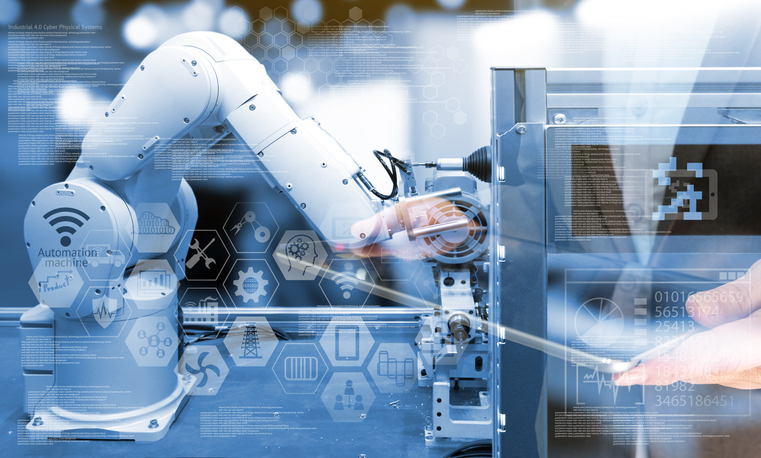
The efficiency of production is increased when the work of the employee does not require unnecessary movements and uncomfortably strained and forced postures, when the work environment is well structured and safe, when working heights and equipment are adequate and so on. Creating the right conditions is also very important from the point of view of the employees. The concept of 'wellbeing' should play a significant role not only in the office but also in an industrial environment because the employees can work more efficiently if the appropriate conditions are secured both for work and during breaks. By taking the above considerations into account and applying the appropriate principles work-related injuries and long-term musculoskeletal disorders (MSDs) can be better avoided and the number of accidents, as well as fluctuation and illness-related absence can be significantly reduced.
During the design of the workplaces and during the coordination of the human, machine and robotics factors from an ergonomic point of view, not only the changes in the technical conditions but also the changes in the labour supply should betaken into account, because the society is increasingly characterized by aging and ethnic diversity. Workers often have very different body sizes and abilities, depending on age and population. Moreover, there are many more women working in the manufacturing industry than in the past and due to their physical characteristics they can only maintain their health during work if the workload is lower. Furthermore, the integration of workers with disabilities or reduced working abilities is becoming increasingly important today. The optimization of the work environment and workflow, as well as the application of profile comparisons make it possible that —considering the capabilities of the employees and the variety of jobs — all employees get the job they are optimally suited for and that they can perform their task with as minimal workload as possible.
Asa result of the phenomenon of digitization, another important aspect should betaken into account, namely the fact that employees, such as engineers from one particular factory, often do their job elsewhere. They may work at home or in another subsidiary of the company, they can even be located in another country.Moreover, the so-called "Gig Economy", a system in which the company collaborates with freelancers, with other small companies or with project-related employees, is gradually becoming more widely spread. These forms of work have all been made possible through the Internet because nowadays there is no obstacle to communication and consequently to the collaboration of people living in geographically remote areas.
TheViveLab Ergo software provides an excellent solution to the problems described above. It is an exquisite tool to simulate and analyze the movements of the workers and thus to ergonomically optimize the working process taking into account all aspects of the working environment. The software works with an anthropometric database that covers the entire world population, enabling the exact simulation and analysis of every employee's movements regardless of the size and body proportions of the employee and the age group or population they belong to. During the ergonomic survey the movements of the employee can be recorded by means of inertial sensors and the analysis of the motion files is carried out by the software according to the integrated ergonomic analysis methods (RULA, OWAS, NASA-OBI, ISO11226, EN1005-4). The results can be displayed in real time. It is also possible to create a PDF report of the detailed analysis by means of a few mouse clicks. The report highlights the positions where action needs to be taken to improve the quality of the workplace.
The ergonomics experts develop an action plan with alternative solutions to correct the problems identified in the analysis report and they select with the customer those solutions that meet the customer’s goals and are practicable as well. Upon request, the entire process, from the inspection in the production area through the recording of motion files up to the formulation of an action plan is carried out by the ergonomics experts. Optionally, they examine which workplaces can be automated and where it is possible to employ aging workers or workers with disabilities.
If someone feels comfortable at the workplace, he/she can work focused, motivated and productive. Even minimal changes to standing or sitting positions can relieve the spine, neck, shoulders, arms and legs. A well-designed workplace that meets ergonomic requirements allows working comfortably and without feeling any pain. Therefore, the goal is to help shorten production cycles, make production processes more efficient and relieve workers by creating a healthy work environment, while facing the challenges of the Fourth Industrial Revolution in the mean time.